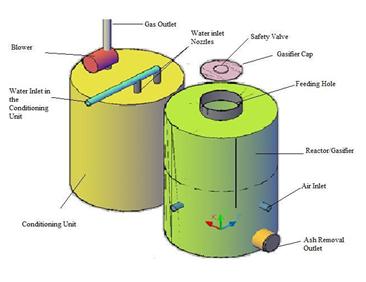 |
Figure 1. Schematic diagram of Gasifier
|
|
Abstract
Energy shortage is the major problem for Pakistan’s Economy. This problem can be solved by using the alternative/renewable sources of energy; the best alternative source of energy is producer or syn gas. There are large amounts of biomass available in our country in the form of crop residue. Pakistan is producing millions of tons of biomass annually in the form of crop residue, rice husk, and wood mills waste, cotton processing waste and corn pith, which can be easily used in the production of syn or producer gas. The research work was conducted in the Workshop, Department of Farm Machinery & power, Faculty of Agricultural Engineering and Technology University of Agriculture, Faisalabad in 2008-09. In this research work fabrication and evaluation of a downdraught gasifier with different solid fuels like Coal, Charcoal and Corn Piths was carried out for 12 kW single cylinder engine. The amount of gas produced by equal weight (18 kg) corn pith was 35 m3, by charcoal was 41m3 and by coal was 39.7m3. This gas was sufficient to operate an engine of 12 kW which require 39.6 cubic meters per hr. the consumption of gas will be reduced when it runs a dual fuel engine (Diesel Engine).
Problem Statement
Pakistan is an agricultural country. In Pakistan almost all the crops are grown. Wheat, Rice, Corn, Sugarcane, Cotton are the major crops grown in the country. These crops are grown on a large area and produce a huge amount of biomass. From these crops we can get a huge quantity of biomass which can be used in the gasifier. Agricultural waste (crop residue) from corn and cotton is best suitable fuel for a gasifier.
Gasification process operates at high temperature and includes the use of oxygen and process steam in conjunction with the fuel. When undertaken with air as oxidizing agent the producer gas has a net calorific value (NCV) of about 46MJ/m3 to 48 MJ/m3. The heating value of this gas makes it suitable for use in the IC engines. When oxygen is used, the producer gas has a NCV of 10-15 J/m3, sufficient for limited pipeline transport and synthesis gas conversion.
Downdraught gasifiers being comparatively easy to build and operate are likely to be most appropriate for our conditions. The design of downdraught gasifier is simple and easy to construct. Producer gas requires no major modifications of existing engines. To fuel existing spark-ignition engines with producer gas requires only a minor replacement or attachment to the carburetion system. Producer gas requires no unconventional technology such as is required by electric, steam or sterling engine-powered motor transport. When we used it in the compression-ignition engine we need only minimum supply of diesel to operate the engine.
Objectives
- To design and fabricate a downdraught gasifier to run 12 kW engine.
- To test and evaluate the gasifier for coal, charcoal and corn pith (Corn Cobs).
Methodology
The fabrication, conversion of solid biomass to gaseous fuel in a downdraught gasifier and evaluation was examined in the Agricultural Engineering Workshop Faculty of Agricultural Engineering and Technology, University of Agriculture, Faisalabad in detail.
The gasifier was made by MS sheet of 16 gauge (1.5875mm) in cylindrical shape of 60.96 cm diameter and 91.50 cm in height. A 10 cm round opening was provided at the top of gasifier for feeding the biomass. A throat with a slope of about 50º (standard) and 7.48 cm diameter at the narrowest section was fastened in the gasifier. Four sided air inlets opposite to each other were provided for air supply in pyrolysis zone at a height calculated according to Hearth Load Concept. A 3.8 cm diameter pipe was provided under the grate for exhaust of producer gas. A 12.7 cm diameter in diameter ash removal hole with air tight cap was provided just above the bottom of gasifier.
For the cooling and cleaning purposes water cooling/cleaning system was used. For this purpose a cleaning unit was designed with dimensions of 61 cm in diameter and 83 cm in height. At the top of this unit, two hollow cone nozzles were installed for shower of water. These were spray water from top on hot raw gas coming from gasifier in the cleaning drum from bottom and were leave the drum from top and the water with impurities was removed from bottom of the unit (Fig.1). In second stage of study, the gasifier was evaluated by using coal, charcoal and pith (corn cobs). It was tested for the temperature and composition of syn gas produced with these fuels. The running time and volume of gas produced by each fuel with same quantity was noted.
Data collected was statistically analyzed using CRD design. PROG GLM (General Linear Mode) procedures of the SAS System (1989) were used to analyze the data. When the F-test indicates statistical significance, treatment means were separated by the LSD test.
Results and discussion
In this research the parameters like production of Carbon dioxide, Carbon monoxide, sulpher dioxide, Nitrogen dioxide, Nitric oxide, running time and volume of gas produced with equal quantity of different types of fuel were tested. The fuels used for this evaluation were Pith (Corn Cobs), Coal and Charcoal.
The data then statistically analyzed on personal computer by using PROG GLM (General Linear Model) procedures of the SAS systems (1989). The following results were obtained at 5% level of significance.
Volume of Gas Produced: The volume of producer gas produced by the gasifier was measured by the following formula
Vol. of Gas Produced = Time (sec) * area of pipe (m3) * velocity of gas (m/s)
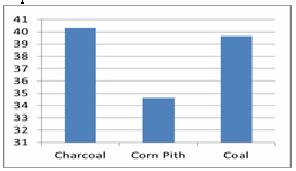 |
Fig 2. Volume of Gas Produced (m3)
|
|
The velocity of the gas leaving the blower pipe was measured with the anemometer and time was recorded with stopwatch.
The Fig.2 reveals that the treatment Charcoal produced the more volume of gas 40.35 m3 as compared to the other treatments. The Coal comes at second number which produced 39.67 m3 of gas and the pith was at third number which produced 34.65 m3 with the same quantity of the fuel. This may be due to the reason that the pith has low bulk density and difference in the calorific values as compared to coal and charcoal. The charcoal, pith and coal have calorific values of 5.95, 6.29 and 4.60 Mj/m3 respectively in the downdraught gasifier.
Carbon Monoxide (CO): Carbon monoxide (CO) is a highly poisonous but combustible gas in the producer gas. Charcoal produced 1137.5 ppm of CO while Pith produced 1166.0 ppm and the coal produced 1017.75 ppm Carbon Monoxide gas in the producer gas.
Carbon Dioxide (CO2): The mean CO2 production in the producer gas was 5.90, 5.00 and 6.52 for charcoal, pith and coal respectively. The production of carbon dioxide in the gasifier is not the property of the fuel; it is only the function of the controlled amount of air supply to the gasifier.
Sulphur Dioxide (SO2): SO2 is a non-combustible, colorless and toxic gas present in the producer gas. Average sulphur dioxide produced with the charcoal was 3756.5 ppm, which was very high as compared to pith (3141.8) ppm and the coal (2700.5) ppm. The mean of the treatments was 2226.26 ppm. This gas may be converted into sulphuric acid after reacting it with water.
Nitric Oxide (NO): The results showed that the charcoal and pith did not produce any nitric oxide in the gasification process while the coal produces a huge amount 216.0 ppm in the producer gas. California Energy Commission investigated that the burning of the pith (Corn Cobs) in the down draught gasifier did not produce any type of nitrogen oxides.
Nitrogen Dioxide (NO2): Charcoal produced the 198.75 ppm NO2 in producer gas and burning of coal as a solid fuel in the downdraught gasifier was yields 69.75 ppm of NO2 in the producer gas. The burning of Corn Cobs did not produce any amount of Nitrogen Dioxide. Schapfer stated that charcoal and coal, when used as a fuel in the downdraught gasifier produces nitrogen oxides up to 60 percent on volume basis.
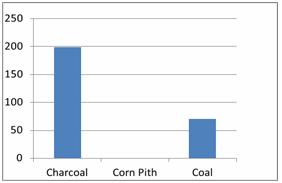 |
Fig.3 Production of Nitrogen Dioxide (ppm)
|
|
Conclusions
- If crop residue or biomass are available in sufficient amount without any danger to forest and animal feed, gasifier can serve as an option for energy supply in remote areas.
- This technology is decentralized energy conversion system which operates economically even for small scale.
- Mixed with air, the producer gas can be used in gasoline or diesel engines with little modification or in burners.
- This technology is very good for adaptation especially for villages, sawmills, rice shelling plants and sugar mills where biomass is in excess quantity.
- The Corn Cobs (pith) can be used without any prior processing. It is cheaper than coal and charcoal and gives almost equal volume of gas as compared to other fuels.
|